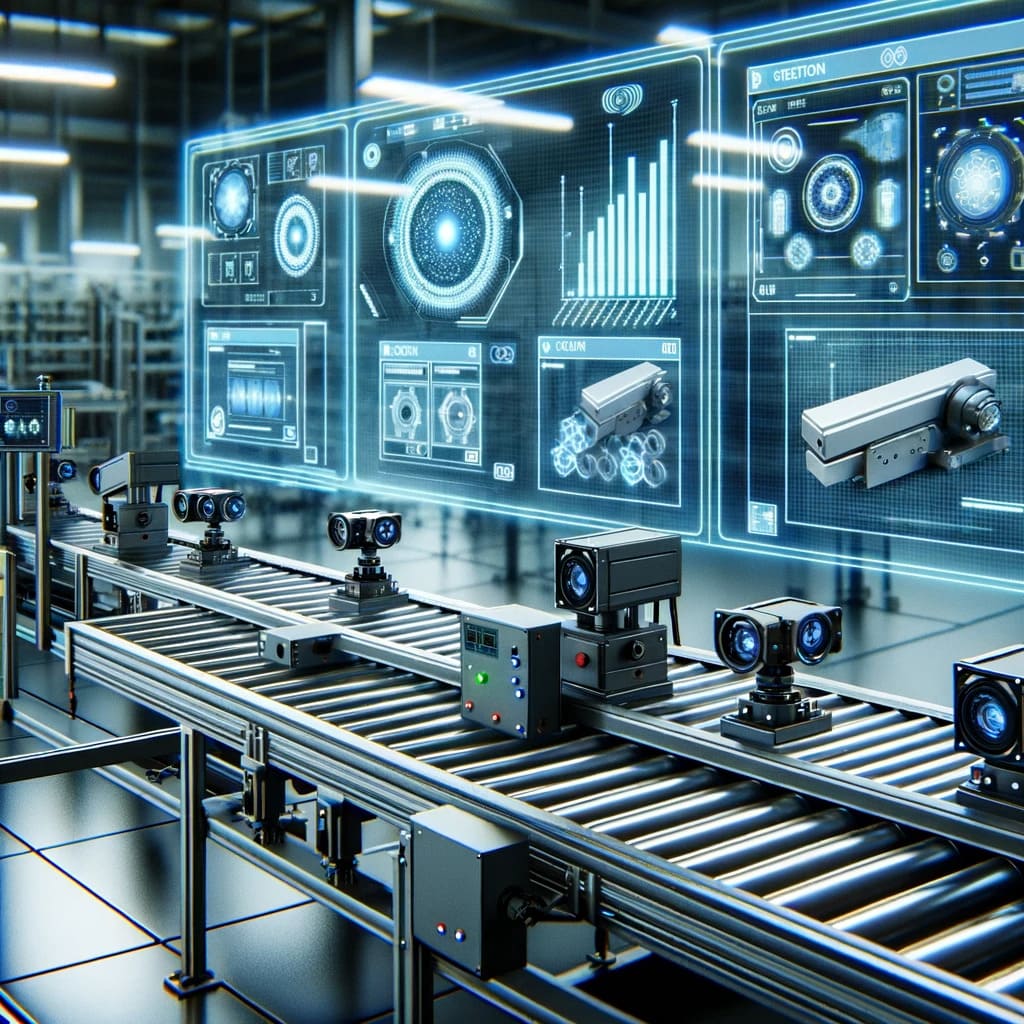
Industries are constantly faced with the challenge of keeping their equipment in optimum working order, especially as it ages or becomes obsolete. Obsolescence is not just a technical issue; it can have a significant impact on a company's productivity and finances. This article provides a guide to developing an action plan that will help you anticipate and manage the obsolescence of your industrial equipment, ensuring optimum performance and reducing the risk of unplanned downtime.
1. Complete Plant Assessment and Analysis
The first step is to carry out a complete audit of your equipment: identifying its age, recognizing parts that are already obsolete or about to become so, and detecting early warning signs of potential breakdowns. Understanding which equipment is vital to your operations enables you to prioritize the actions you need to take.
2. Proactive anticipation strategies
Anticipating obsolescence requires strategic planning, including the sourcing of spare parts, the creation of appropriate inventories and the implementation of a technology watch to keep abreast of developments likely to affect your equipment.
3. Preventive Maintenance and Planning
Developing a schedule for preventive maintenance and progressive parts replacement can significantly reduce the risk of unexpected failures. Financial planning for parts purchasing and maintenance scheduling can also minimize the impact on production.
4. Retrofit and modernization
Consider retrofitting or modernizing your plant as an alternative to purchasing new equipment. This approach can not only extend the life of your equipment, but also make it more efficient and in line with current standards.
5. Working with a reliable supplier
Choosing a trusted partner for spare parts supply is crucial. A responsive, reliable supplier can make all the difference by minimizing downtime through rapid delivery, and guaranteeing the quality and durability of the parts supplied.
Conclusion
Industrial equipment obsolescence represents a major challenge, but with the right planning and strategy, it's possible to minimize its negative impact. A well-designed action plan to anticipate and manage obsolescence ensures production continuity and efficiency, while controlling costs. By integrating assessment, prevention, planning, modernization and strategic collaboration with reliable suppliers, your company can transform obsolescence into an opportunity to improve and optimize industrial operations.